Pour assurer sa production de confiserie, la société écossaise Hannah’s Sweets devait jusqu’ici vider manuellement ses matières premières en sacs, à un rythme de 300 sacs par jour. Elle a fait appel au fabricant Flexicon pour automatiser et sécuriser son installation.
Hannah’s Sweets produit une large gamme de bonbons, notamment les « Snowies Jazzies », des disques de chocolat recouverts de morceaux de bonbons colorés. Pour mener à bien sa production, l’entreprise transforme chaque semaine 50 à 60 tonnes de sucre, de lait en poudre, de lactosérum en poudre, de farine de blé et d’autres ingrédients secs. Chacun des ingrédients est reçu en sacs de 25 kg. Hannah’s Sweets utilise près de 300 sacs par jour, vidés à une cadence de 1 975 kg/h.
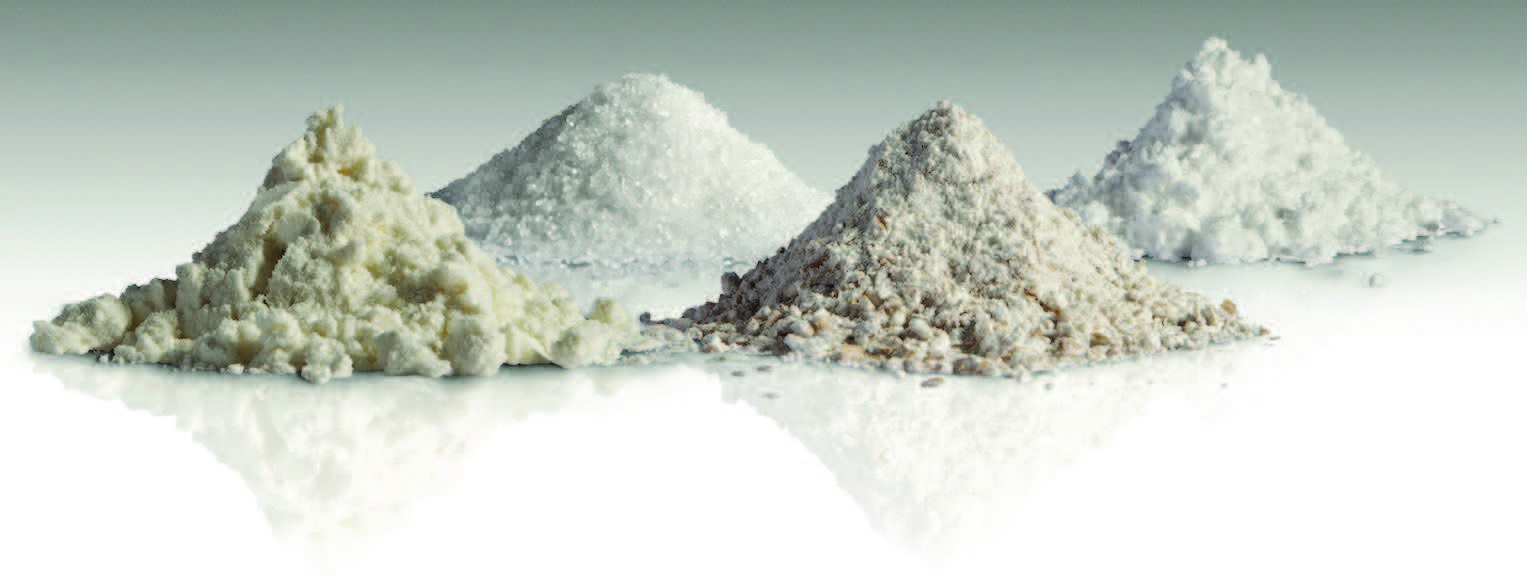
La recherche d’une offre complète
Dans son cahier des charges, Hannah’s Sweets souhaitait réduire la manipulation manuelle des sacs, réduire la poussière et éviter que les palettes soient véhiculées dans la salle de process hygiénique. Après avoir contacté Flexicon, elle a décidé d’installer une station de vidage de sacs du fabricant, ainsi qu’un système de transport pneumatique intégré avec un convoyeur à rouleau et un palonnier. Le système de livraison devait traiter des matières dont la densité apparente était de 208 kg/m3 pour le lait en poudre et jusqu’à 705 kg/m3 pour le sucre granulé. Le directeur général de Hannah’s Sweets, Tom Munro, témoigne : « Flexicon a proposé un système clés en main pour gérer tous les ingrédients, alors que d’autres ne pouvaient fournir que certaines parties du process ».
Aspiration de la poussière
À l’aide du poussoir sous vide, un opérateur déplace les sacs des palettes vers le convoyeur à rouleaux, qui les transporte au travers d’un passage mural dans la salle de mélange où se trouve la station de vidage de sacs Flexicon. Équipée d’un ventilateur d’aspiration à grande vitesse, l’unité aspire la poussière en suspension générée par le processus de déversement manuel loin de l’opérateur, sur deux filtres à cartouche ayant une superficie combinée de 9 m3. L’accumulation de poussière sur les surfaces extérieures du filtre est délogée sur un cycle chronométré, en alternant les souf#es d’air provenant des buses situées à l’intérieur de chaque filtre, maintenant l’efficacité de la collecte de la poussière. La poussière délogée tombe ensuite dans la trémie d’une capacité de 140 litres, éliminant ainsi les déchets.
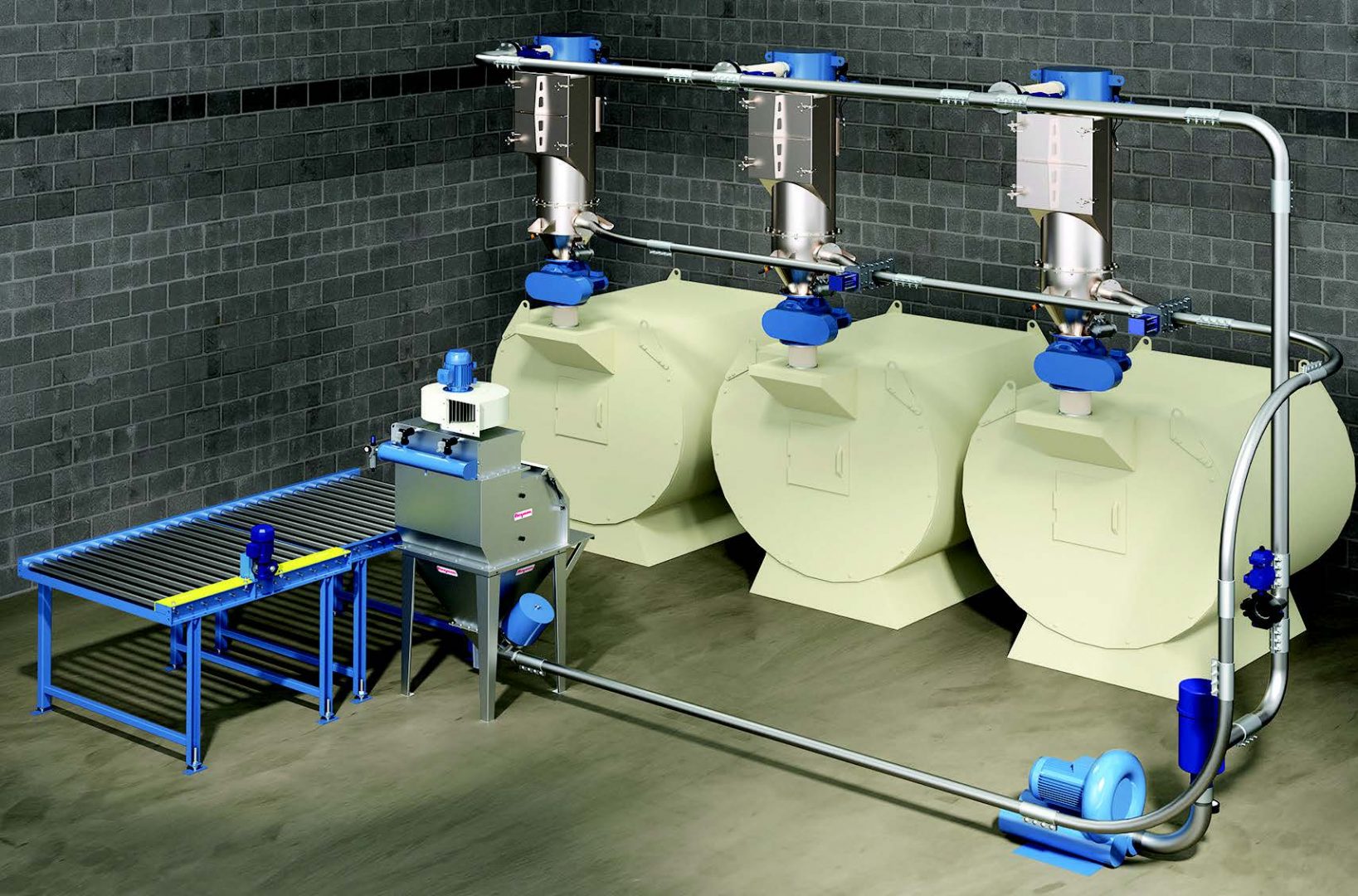
Installation du pneumati-con
La matière première est acheminée via un adaptateur de ramassage monté sous la base de la trémie, dans le système de transport pneumatique Pneumati-Con développé par Flexicon. Alimenté par un ventilateur de 7,5 kW, il transporte les ingrédients à travers une conduite de 12 mètres de long et 75 mm de diamètre, avec trois vannes de dérivation à commande pneumatique qui alimentent séquentiellement trois filtres récepteurs de 450 mm de diamètre, chacun alimentant un réservoir de mélange séparé. Une fois séparé du flux d’air, le produit est dosé à travers la vanne rotative du récepteur du filtre dans une trémie de pompage de 28 litres, qui se décharge dans un réservoir de mélange, où les ingrédients secs sont mélangés avec des graisses végétales. Le composé de chocolat liquide ainsi produit est mis sous diverses formes en utilisant un équipement de moulage automatique.
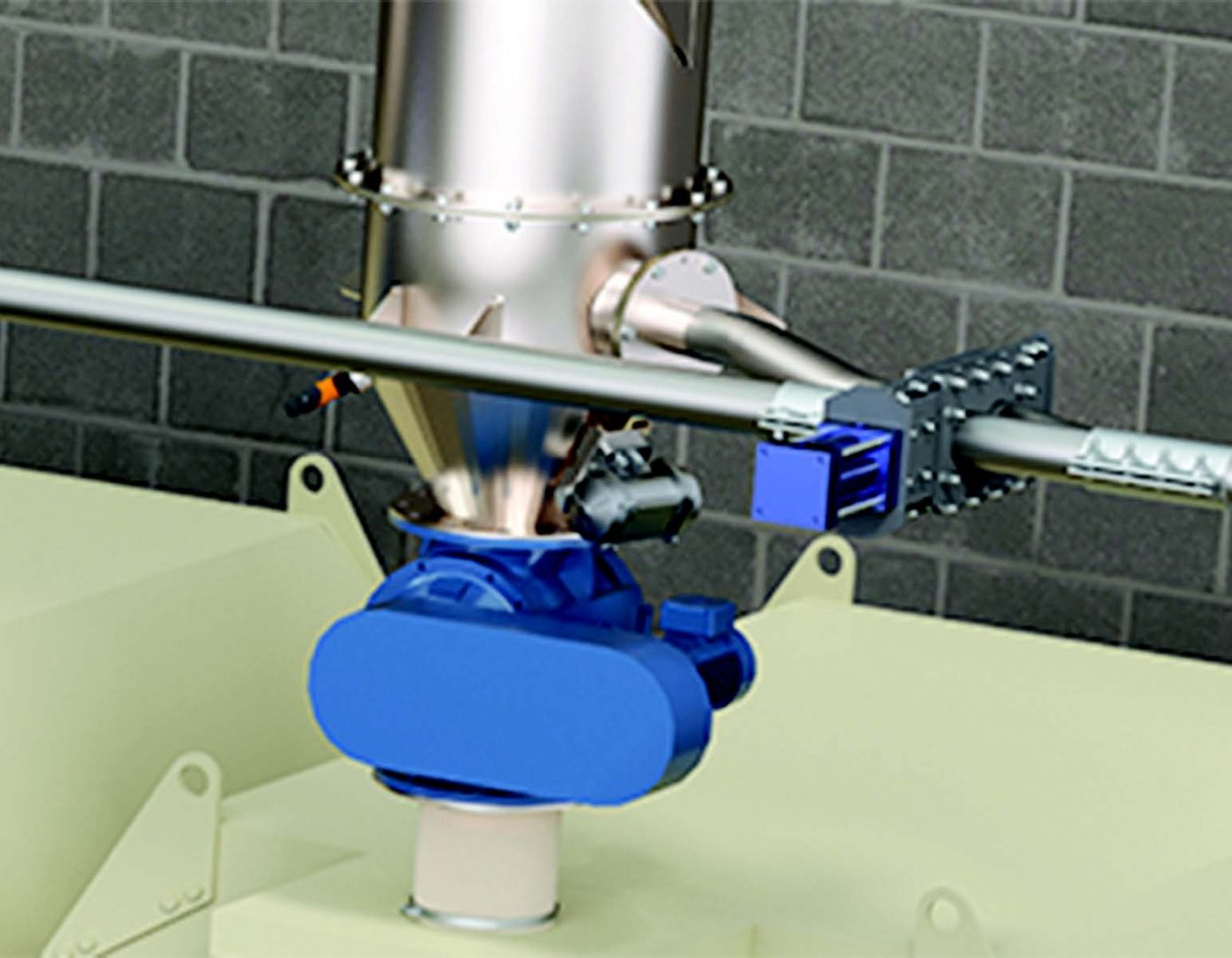
Sécurité et nettoyage
Le système fermé proposé par Flexicon empêche la contamination du produit et de l’environnement de l’usine, tandis que le ventilateur pneumatique évacue la ligne de transport. Cela écarte le besoin de rincer le système pendant les changements de matières et garantit que tous les ingrédients du lot atteignent les réservoirs de mélange. Cela élimine ainsi les déchets. « Nous avons une politique de nettoyage au fur et à mesure, mais le nouveau système de livraison ne nécessite qu’un nettoyage quotidien par les opérateurs », déclare Tom Munro. Depuis son installation, le système a été fiable, offrant des performances constantes. « Les lignes fonctionnent depuis un an et nous n’avons eu aucune opération de maintenance à effectuer », conclut Tom Munro.
CONTRÔLE PAR AUTOMATE PROGRAMMABLE
Le système est contrôlé par un automate programmable qui ouvre et ferme chaque vanne de dérivation ou démarre et arrête chaque vanne rotative lorsque les signaux sont reçus des capteurs de niveau haut de chaque trémie. Il peut arrêter le ventilateur du système de transport lorsqu’un signal est reçu du niveau bas de la station de vidage de sacs. Les cuves de mélange sont remplies jusqu’à un poids de lot combiné de 2 à 3 tonnes de chocolat liquide.