Transport en phase dense
AZO propose aux industriels du vrac son système VacuumPlus qui garantit une manipulation douce du produit, une absence de ségrégation et des économies d'énergie. Frédéric Loiseau, directeur commercial de la société, revient sur les fondamentaux du transport en phase dense et présente la solution.
Pourquoi avez-vous toujours privilégié le transfert par aspiration ?
Frédéric Loiseau : Chez AZO, nous nous sommes toujours focalisés sur le transfert par aspiration car il permet de garantir une propreté maximale dans les process. Il évite par nature les émanations de poussière et permet de réaliser des installations en totale conformité avec la réglementation ATEX. Nous avons d’ailleurs fait partie des premières entreprises à industrialiser le transfert par aspiration. Nous optimisons constamment nos équipements pour répondre au plus près des besoins des clients. Nos ingénieurs décryptent le fonctionnement scientifique du transport pneumatique et, avec leur expertise, développent des équipements innovants. Nous cherchons à aller toujours plus loin dans l’analyse du comportement des pulvérulents, ces derniers pouvant être sensibles et complexes à transporter.
Sur quel critère distinguons-nous la phase dense de la phase diluée ?
F. L. : Le principe de fonctionnement du transfert pneumatique peut être grossièrement illustré de cette manière : nous transportons des kilos de poudres avec des kilos d’air. Plus le transfert pneumatique sera chargé, plus nous nous approcherons d’une phase dense. D’un point de vue scientifique, nous pouvons considérer que tous les systèmes qui fonctionnent au-delà de 30 kg de produits par kilo d’air sont en phase dense. En fonction des produits, les ratios air/produit peuvent être beaucoup plus importants, jusqu’à 90 kg de produits par kilo d’air.
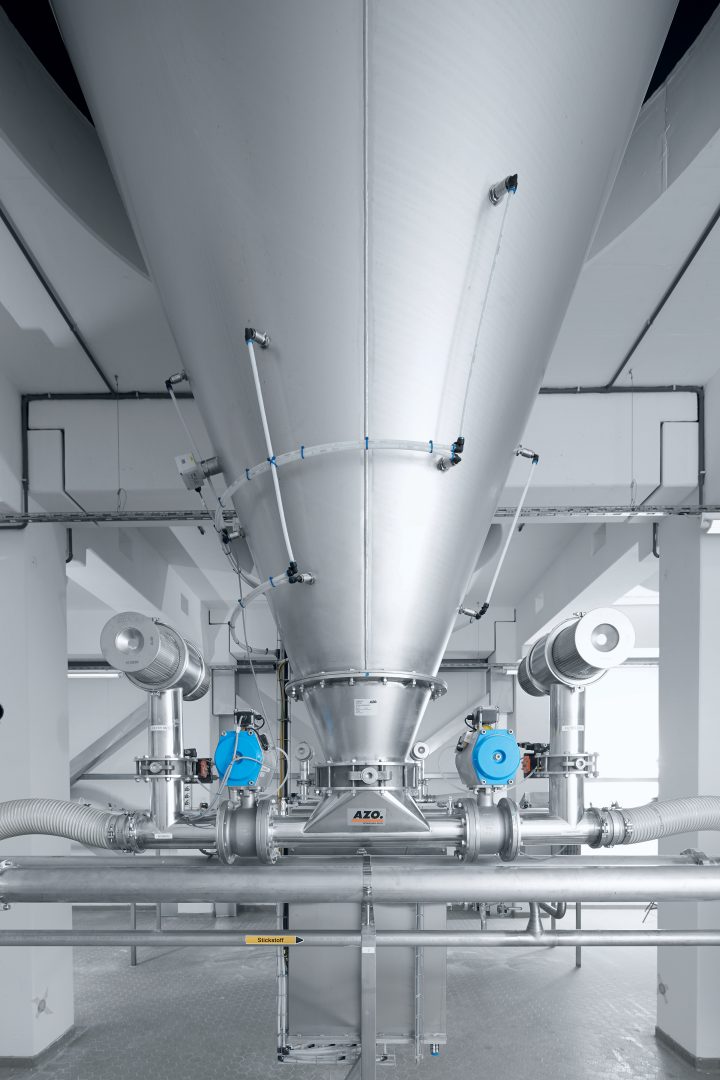
En quoi le transport en phase dense optimise-t-il le traitement de l’air ?
F. L. : Certains pulvérulents requièrent un traitement de l’air de transport. En cas de produits thermosensibles, cela permet par exemple d’éviter les mutations de calories de l’air vers le produit. En cas de produits hygroscopiques, cela peut également permettre d’éviter les mutations d’eau de l’air vers le produit. Pour anticiper ces mutations, le traitement de l’air assure un abaissement de la température ou du taux d’humidité de l’air de transport. Le traitement de l’air étant relativement coûteux, le transfert en phase dense s’avère très intéressant : il permet de transporter davantage de produits avec moins d’air, ce qui permet de réaliser des économies en termes de traitement de l’air. En phase dense, un industriel traite a minima trois fois moins de volume d’air qu’avec un transport pneumatique classique.
Quel est l’intérêt d’un transport à basse vitesse ?
F. L. : Un transfert classique en phase diluée s’opère en moyenne avec un ratio air/produit de 10 kg de produits par kilo d’air, à une vitesse moyenne de 22 m/s. Avec un transfert pneumatique en phase dense, la vitesse de transport peut être rabaissée à son minimum : selon les caractéristiques du produit, ces vitesses peuvent osciller entre 1 et 5 m/s. En diminuant la vitesse, on diminue également l’attrition. Le système entraînera moins d’actions mécaniques, ce qui permet de préserver davantage le produit final. Cela est vrai pour des produits plutôt fragiles, de type poudres de café, de lait ou de chocolat, mais aussi pour des flocons. La phase dense permet de ne pas endommager la taille des particules.
Ne risque-t-on pas le démélange des matières ?
F. L. : Lors du transport en phase fluide avec de grandes vitesses d’air, on aura tendance à constater une séparation des produits. Cela peut être problématique lorsque plusieurs produits forment un mélange : il est très important d’éviter la ségrégation lors du transport d’un mélangeur vers un point de transformation par exemple. La phase dense permet non seulement une densification, et donc des particules qui se tiennent mieux entre elles, mais aussi une diminution de la vitesse qui évite aux particules de plus grande taille de s’envoler plus rapidement.
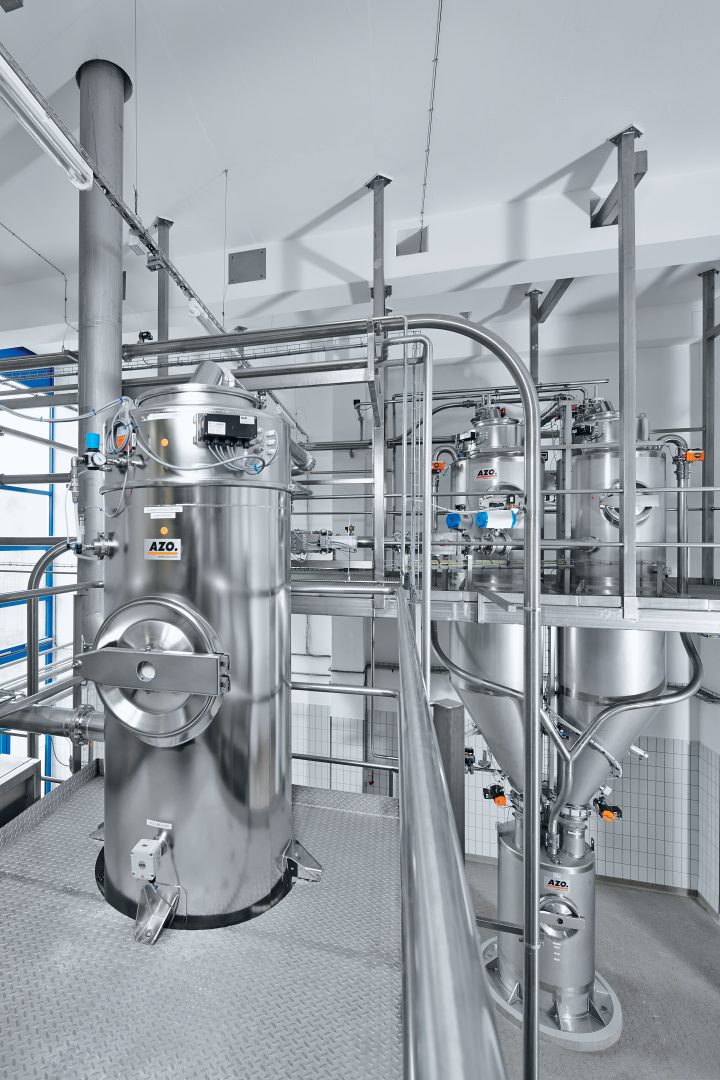
Quelle est la particularité de votre système VacuumPlus ?
F. L. : La grande difficulté rencontrée par les industriels du vrac est que les ingrédients ne se ressemblent pas et n’ont pas les mêmes comportements. Le matériel utilisé doit donc être capable de gérer ces différences. Nous avons alors travaillé au développement d’équipements les plus universels possibles. Pour assurer la fiabilité du système VacuumPlus, AZO a imaginé un nouveau processus : l’adjonction d’un réseau d’air parallèle au réseau de transfert. Autrement dit, nous mettons à disposition du transfert un réseau de réinjection d’air tout au long de la tuyauterie ; ces réinjections se faisant de manière proportionnelles grâce à un système de vannes couplées à des pressostats. L’idée est d’obtenir une lecture de la pression tout au long du circuit et de piloter des courbes grâce aux réinjections. Lorsque la variation de pression est anormale, nous réinjectons de l’air dans la proportion nécessaire afin de lisser une courbe de transport. Ainsi, il est possible de corriger la courbe de pression et de vitesse au gré du transport et des changements de produits. Nous pouvons alors dire que le système, disponible pour des distances jusqu’à 100 mètres, est auto-adaptatif. Chez AZO, notre métier est de proposer des systèmes clés en main, incluant la partie électrification, automation et pilotage de l’installation : le VacuumPlus est donc naturellement livré avec son coffret, qui permet à l’opérateur de paramétrer son système.
Auriez-vous un exemple d’application possible pour ce système de transfert ?
F. L. : Le transfert par aspiration est beaucoup utilisé pour alimenter les machines de conditionnement. Dans un process de fabrication, les poudres sont à un moment ou à un autre stockées : elles doivent ensuite être convoyées du stock tampon jusqu’aux lignes de conditionnement. Sur ce convoyage, nous retrouvons souvent un point d’arrivée, mais plusieurs points de départ. Il est en effet rare qu’une machine de conditionnement ne conditionne qu’un seul et unique produit. Le transport par aspiration a la particularité de pouvoir s’adapter. Nous retrouvons un point d’aspiration unique avec une tuyauterie qui ira chercher sous chacun des éléments de stockage les produits. Le flux produit est ainsi réduit à son strict minimum.