Semences
Les méthodes de plantation à grande vitesse ont augmenté les besoins en lubrifiants pour l'écoulement des graines, comme l'EZ-Slide, fabriqué par Van Sickle Paint Manufacturing, une entité de Diamond Vogel située à Orange City aux États-Unis. Cette entité a dû revoir son process.
Les formulations développées par Van Sickle améliorent la plantation des semences en réduisant l'électricité statique et l'humidité, qui provoquent le « pontage » des graines. « Les agriculteurs versent ce produit avec leurs graines pour les enrober afin qu'elles ne s'agglutinent pas, explique Tom Hubers, ingénieur de projet chez Flexicon. Cela permet à tout de mieux se planter. » Les produits existent en trois versions : une poudre de graphite, une poudre de talc et un mélange talc-graphite. Van Sickle s'est lancée dans le secteur des lubrifiants il y a dix ans. Auparavant, les opérateurs déversaient des sacs de 22,5 kg de graphite et de talc dans un mélangeur. « Ils pré-étiquetaient des conteneurs de différentes tailles dans une pièce, puis les apportaient dans une autre pièce pour les remplir un par un, explique Tom Hubers. Ils plaçaient le récipient sous le remplisseur, puis lançaient le cycle de remplissage manuellement. Il s'agissait d'une opération nécessitant beaucoup de main-d'œuvre. »
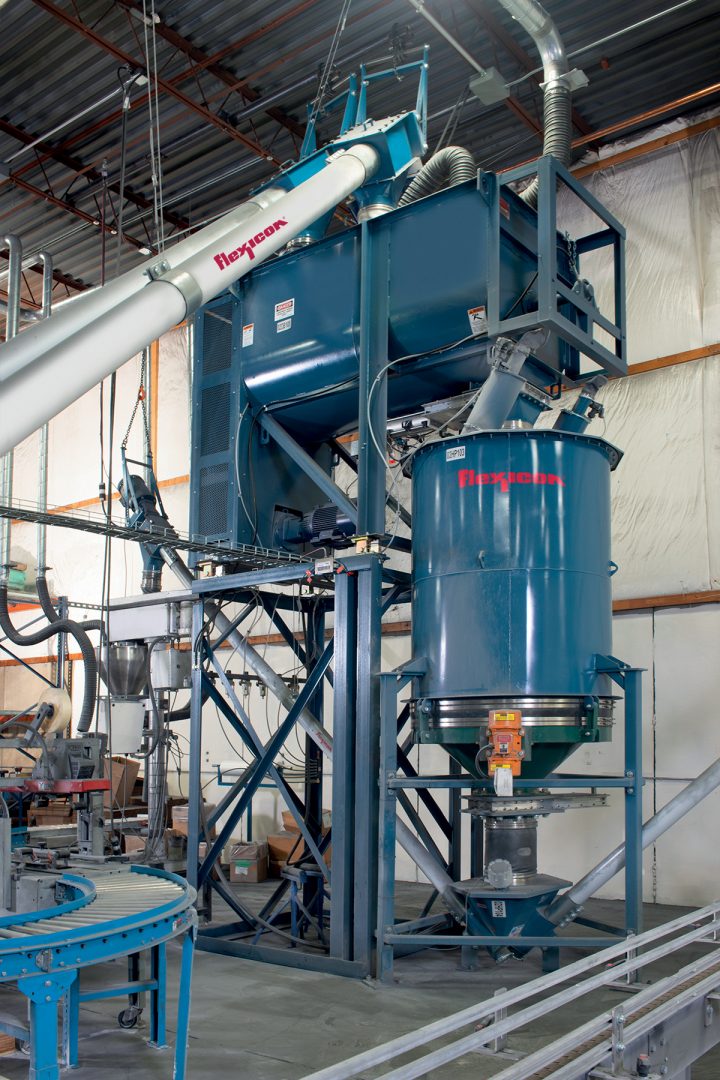
Optimisation du conditionnement
Afin d'automatiser ses opérations de conditionnement et d'augmenter ses capacités de production, Van Sickle a acquis un nouvel entrepôt et centre de distribution en 2020 : la moitié de celui-ci est consacrée au conditionnement des lubrifiants pour semences. Outre les gains d'efficacité obtenus par l'automatisation, le nouveau système mis en place permet à l'entreprise d'acheter du talc et du graphite dans des big bags d'une tonne, à un coût inférieur à celui des sacs de 23 kg. Les matières sont maintenant manipulées, depuis le déchargement de big bags jusqu'au mélange et au conditionnement final, à l'aide de trois déchargeurs BULK-OUT® modèle BFC et de cinq convoyeurs à vis flexibles, tous fournis par Flexicon.
Intégration de trois déchargeurs
L'un des déchargeurs alimente une ligne de conditionnement qui remplit le graphite dans des récipients de 0,45 et 2,25 kg. Les deux autres déchargeurs (l'un pour le graphite et l'autre pour le talc) acheminent le produit vers un mélangeur, qui se déverse dans une trémie tampon. De là, le mélange est acheminé vers deux lignes de conditionnement, l'une remplissant des contenants de 3,5 kg et l'autre des boîtes de 9 et 18 kg. Les big bags de graphite et de talc sont stockés près de l'atelier de production afin d'être acheminés rapidement vers les déchargeurs, dont chacun est équipé d'un cadre de levage de sacs et d'un palan électrique qui se déplacent sur une poutre en porte-à-faux, permettant de hisser les sacs sans utiliser de chariot élévateur. Une fois les sangles du sac accrochées au cadre de levage, l'opérateur utilise une télécommande pour soulever l'ensemble, le positionner dans le cadre et l'abaisser. Ici, un anneau de verrouillage SPOUT-LOCKTM au-dessus d'un tube télescopique TELE-TUBETM à commande pneumatique relie solidement la goulotte de déchargement du sac, après quoi le tube télescopique exerce une tension continue vers le bas sur l'anneau et la goulotte lorsque le sac se vide et s'allonge, favorisant le flux et la vidange.
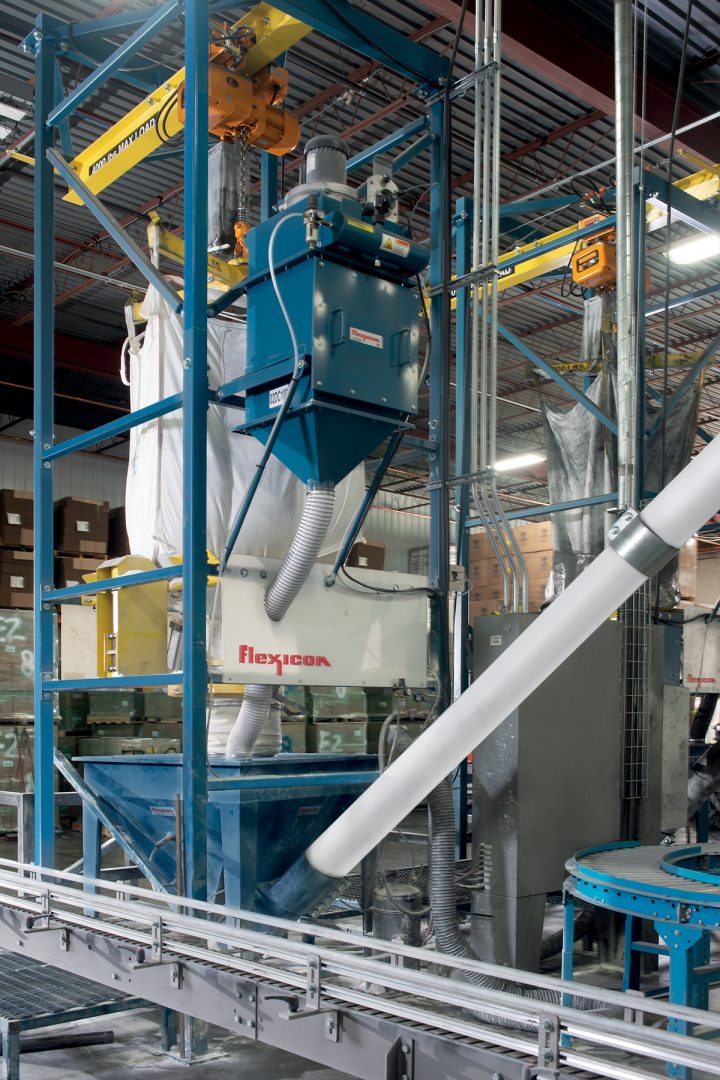
Convoyage par vis flexible
Le déchargeur dédié à l'alimentation d'une ligne de remplissage de graphite déverse le produit dans une trémie de 566 litres, qui charge un convoyeur à vis flexible de 4,5 m de long et de 114 mm de diamètre, lequel est orienté vers la trémie d'alimentation de la ligne de conditionnement selon une inclinaison de 45°. La vis est la seule partie mobile en contact avec le produit. Elle est entraînée par un moteur électrique placé au-dessus du point de déchargement, ce qui évite tout contact du produit avec les joints. Un capteur de niveau haut situé sur la trémie déclenche une alarme sonore indiquant le moment auquel il faut remplacer le sac, tandis qu'un capteur de niveau bas empêche le convoyeur de fonctionner dans un état de « manque ». Les deux déchargeurs dédiés aux produits de talc et de talc-graphite partagent les mêmes caractéristiques que le déchargeur de graphite seul, mais ils utilisent des convoyeurs à vis flexibles de 7,6 m de long et 219 mm de diamètre, également inclinés à 45°, qui se déchargent dans un mélangeur monté sur des cellules de pesée. Les déchargeurs et les convoyeurs fonctionnent en alternance pour atteindre le rapport talc ou talc-graphite et poids cible souhaité, généralement 340 kg. « Nous pouvons choisir la taille de lot et le rapport de mélange que nous voulons, et le système de commande distribue automatiquement les produits », explique Tom Hubers. Le débit élevé des convoyeurs à grand diamètre raccourcit les temps de cycle.
Assurer le bon écoulementBien que le graphite et le talc s'écoulent librement, ils ont tendance à se tasser et à former des ponts pendant le stockage. Par conséquent, chaque déchargeur comprend trois mécanismes pour favoriser l'écoulement : des activateurs de sac FLOW-FLEXERTM qui soulèvent et abaissent les bords inférieurs opposés du sac en forme de V, un vibreur monté sur la paroi extérieure de la trémie sous le déchargeur et un agitateur dans la trémie. Tous démarrent et s'arrêtent automatiquement en synchronisation avec le fonctionnement des déchargeurs et des convoyeurs.
Automatisation du process
Dans le cadre du contrôle de dosage, les cellules supportant le mélangeur s'interfacent avec l'automate du déchargeur pour faire fonctionner et arrêter le convoyeur. Lorsque le poids du talc ou du mélange graphite-talc approche les 22,5 kg du poids cible, le convoyeur ralentit sa vitesse puis s'arrête immédiatement avant d'atteindre le poids cible, de manière à tenir compte du produit encore en suspension, ce qui permet d'obtenir des lots précis et reproductibles. En fin de cycle de mélange, le talc ou le mélange talc-graphite s'écoule par gravité dans une trémie de 2 265 litres. Deux convoyeurs à vis flexibles de 4,5 m de long et 114 mm de diamètre assurent le transfert du produit. Orientés à l'opposé l'un de l'autre, ils transfèrent la poudre vers les lignes de conditionnement pour les contenants de 3,5 kg, et les boîtes de 9 et 18 kg. Comme les cycles de pesage, de dosage et de mélange se répètent successivement, la trémie d'alimentation n'est jamais vide et le fonctionnement est continu. Le talc et le graphite étant tous deux très volatils et sujets à la formation de poussière, chaque déchargeur est ventilé par un dépoussiéreur BAG-VACTM : il contient la poussière en suspension dans l'air pendant le déchargement et écrase les sacs avant de les fermer et de les retirer. « Dès que le système a fini de remplir un lot, il prépare le lot suivant, explique Jason Vore, responsable de l'ingénierie des procédés chez Van Sickle. Nous mettons en marche le système d'aspiration. Nous aspirons tout ce qui se trouve dans le big bag, nous le refermons, nous changeons de sac et nous recommençons. À plein régime, nous changeons un sac toutes les 25 ou 30 minutes. »
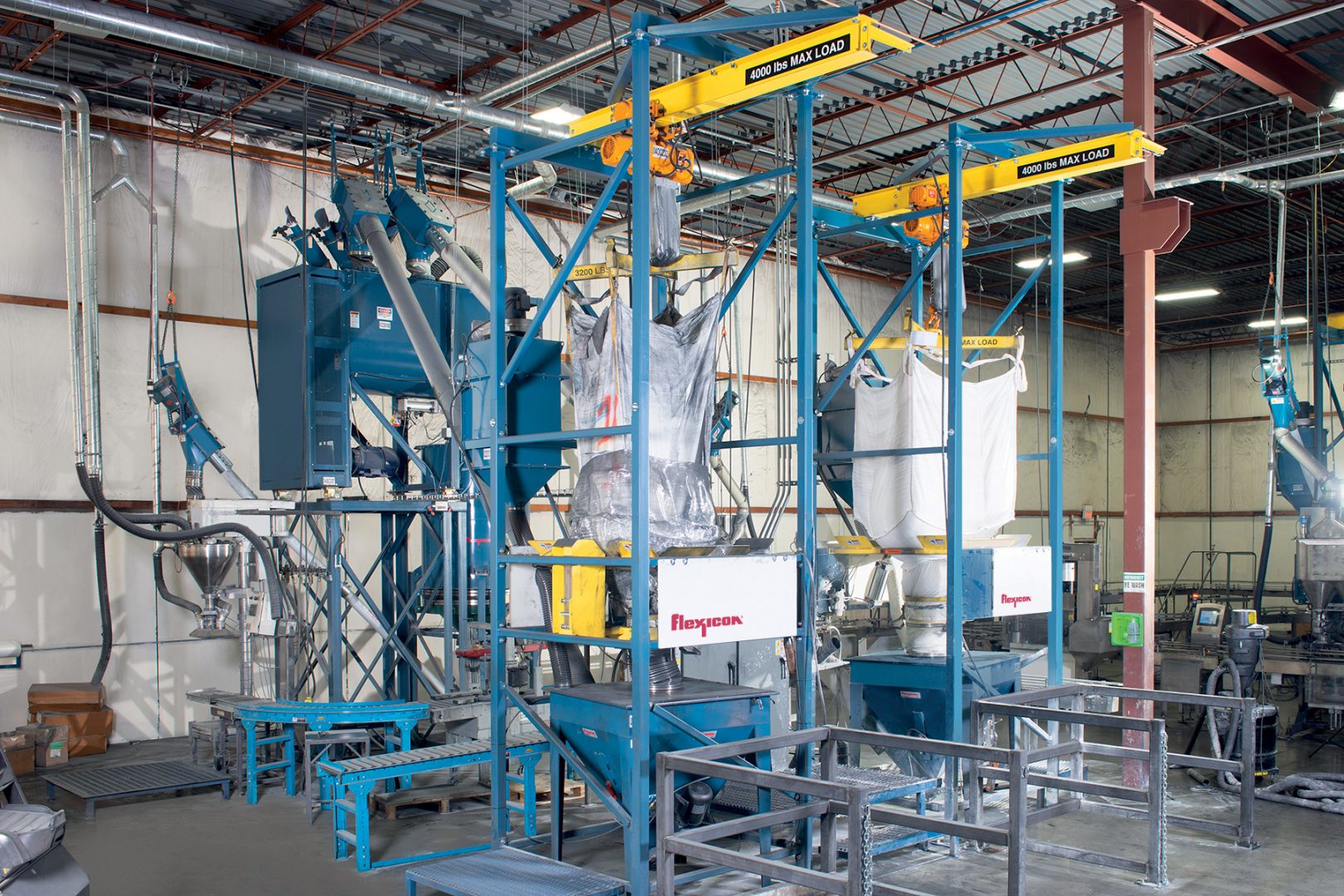
Augmenter du débit
Le débit global du système est de trois à quatre fois supérieur à celui de l'ancienne installation. « Nous pouvons produire autant de contenants de 0,45 kg en une seule journée que nous le faisions en une semaine de 40 heures, explique Jason Vore. Notre rendement horaire a presque triplé. » Désormais, deux ou trois personnes seulement s'occupent de l'opération de conditionnement, et la charge la plus lourde qu'elles soulèvent est un carton de 14,5 kg de produit fini. « Le confort pour l'utilisateur et la propreté de la nouvelle installation sont bien meilleurs, affirme Tom Hubers. Ce n'est en rien comparable avec la précédente installation. »